As data centre infrastructures evolve, the challenge of accommodating higher per-rack power densities becomes increasingly prominent.
Traditional cooling systems, such as raised floors paired with perimeter Computer Room Air Conditioning (CRAC) units, were typically designed to support around 3kW per rack.
However, with modern IT equipment exceeding these densities (often exceeding 10–15 kW per rack), it’s imperative to optimize existing cooling solutions to meet current demands.
Rather than undertaking costly renovations, data centre operators can significantly improve cooling efficiency and capacity by implementing Aisle Containment solutions.
Implementing Aisle Containment is a proven strategy to enhance cooling efficiency and support higher rack densities. By segregating cold supply air from hot exhaust air, aisle containment minimizes air mixing, leading to more consistent inlet temperatures and improved CRAC unit performance. This separation not only eliminates hotspots but also increases the return air temperature to CRAC units, thereby enhancing their cooling capacity.
Key Benefits of Aisle Containment
- Improves cooling efficiency by physically separating hot and cold air streams.
- Increases CRAC performance by raising return air temperatures, unlocking up to 24% more usable capacity.
- Supports higher rack densities without expanding the physical footprint.
- Reduces energy costs—for every 1°F (0.56°C) increase in server inlet temperature, cooling energy use can drop by 4–5% (per ENERGY STAR).
Types of Containment
Both hot aisle containment (HAC) and cold aisle containment (CAC) effectively manage airflow, but the optimal choice depends on specific data centre configurations.
- Hot Aisle Containment (HAC):
Encloses hot exhaust air, directing it back to CRAC units. - Cold Aisle Containment (CAC):
Encloses the cold intake aisle to protect supply air.
Both strategies are effective, evaluating the existing layout, rack arrangement, and cooling infrastructure is essential to determine the most suitable approach
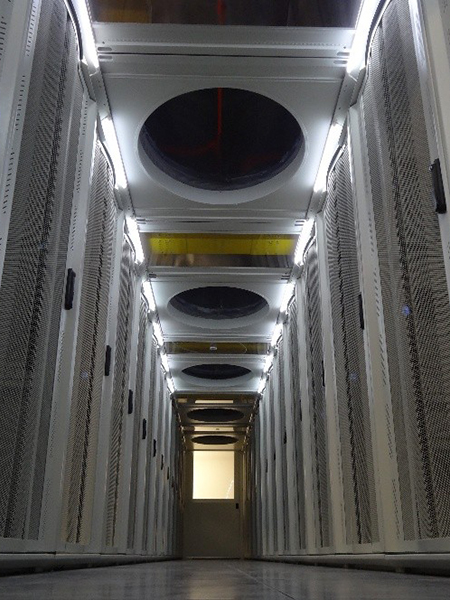
HAC
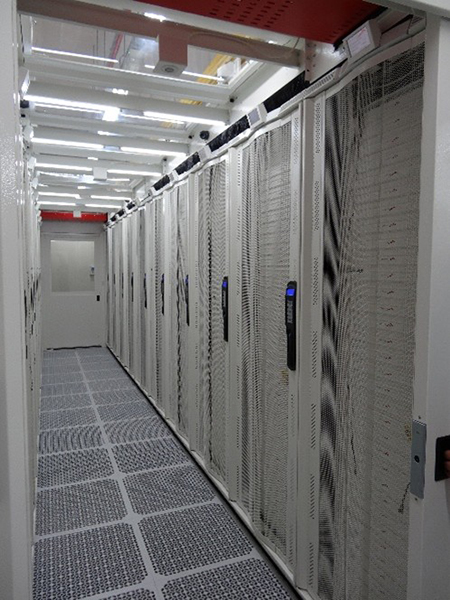
CAC
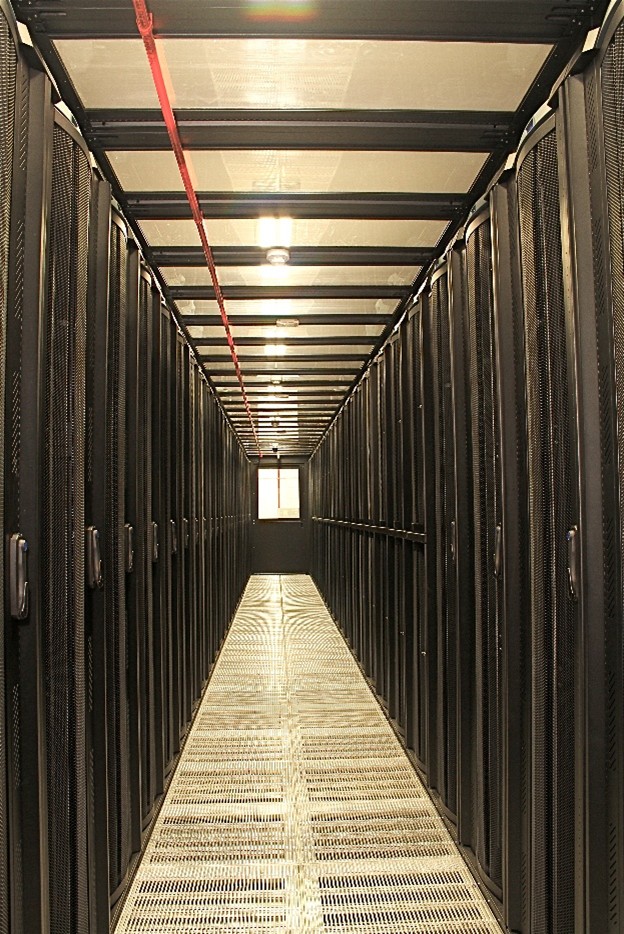
Return Air Temperature
One of the most critical but overlooked factors in cooling efficiency is return air temperature, the temperature of the air returning to the CRAC units.
Recommended return air temperatures are typically between 24°C to 35°C (75°F and 95°F) for maximum CRAC efficiency.
Aisle containment allows return air temperatures to rise, unlocking the full potential of cooling units without physical upgrades.
Project Considerations
Containment systems rarely exist in isolation. Several supporting upgrades may be required for a successful deployment:
Assess Your Rack Configuration
The feasibility and complexity of containment depend heavily on your rack layout:
- Homogeneous environments (uniform rack size and alignment):
Easier to deploy with off-the-shelf containment solutions. - Heterogeneous environments (variable rack sizes and spacing):
Require customized solutions and may necessitate physical reconfiguration.
Assess your willingness to modify rack footprints or layouts before selecting a containment system.
Sharing this with potential vendors ensures accurate system proposals tailored to your facility.
Fire Suppression
Fully enclosed aisles can disrupt fire detection and suppression coverage. You may need:
- Additional smoke sensors inside the contained aisle
- Repositioning or adding sprinkler heads or clean agent nozzles
Engage your fire safety consultants early to avoid compliance issues and hidden costs.
Environmental Monitoring
Prior to adjusting temperature settings, implement real-time monitoring at equipment inlets. This data is vital for making informed decisions about temperature management and ensuring equipment safety.
According to ENERGY STAR, for every 1°F (0.56°C) increase in inlet air temperature, data centres can reduce cooling energy consumption by 4–5%.
Best practice:
- Install sensors before containment to establish a baseline.
- Post-installation, adjust CRAC supply air temperature upward in 0.5–1°C (1–2°F) increments.
- Continuously monitor inlet temperatures to ensure thermal safety.
These sensors can be integrated via DCIM software or independent monitoring systems.
CRAC Unit Controls
Legacy CRAC systems often operate independently, causing inefficiencies like “dueling CRACs” where one-unit cools while another reheats.
Implementing a centralized control system allows units to coordinate temperature and humidity more efficiently, optimizing performance post-containment.
Sealing Gaps and Using Blanking Panels
Containment effectiveness is undermined by unsealed floor cutouts or empty rack slots.
Implement:
- Blanking panels in all unused rack spaces
- Brush grommets or sealed tiles at floor cutouts
This prevents unwanted air mixing and maintains the separation of hot and cold air streams.
Key Take-Aways
Aisle containment is a proven strategy to:
- Support higher rack densities (10–15 kW per rack or more).
- Regain lost cooling capacity.
- Extend the life of legacy infrastructure.
At Cannon Technologies, we specialize in delivering tailored aisle containment solutions that align with the unique requirements of each data centre.
Our expertise ensures that your facility can efficiently handle increased power densities while maintaining optimal thermal performance.